M1® Business Management System
Applied Fab & Machiningleverages the M1® Business Management System to keep your projects on track and on time.
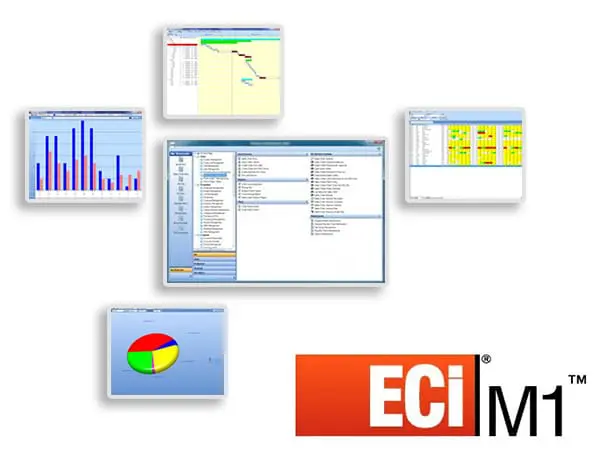
Contact Management
- Document specific contact details for all customers and suppliers, including email and internet addresses
- Manage multiple related locations and individual contacts
- Create tasks and appointments by contact
- View product availability by quantity on hand, in production and on order for a selected part
- Link finance companies and/or resellers to a customer
Order Management
- Track all details and transactions relating to a specific order
- Create jobs for make-to-order items
- Improve on-time delivery performance by managing sales orders
- View multiple orders at once to plan production demands more efficiently
- Manage blanket orders by creating multiple releases for order details
- Automatically create backorders when partially completed orders are shipped
- E-mail order acknowledgements directly to customers
Job Management
- Automatically updates job costs with every job transaction
- Update raw material demands automatically with each job
- Compare estimated job costs to the actual costs as the job progresses
- Manage complex production jobs with multi-level bills-of-materials
Inventory Management
- Control raw materials, finished goods and sub-assemblies
- Ensure accurate stock records through automatic allocations, stock receipts and issues
- Obtain accurate stock valuations
- View future demands on your inventory
- Track standard, average and last costs for all parts
- View the method of manufacturing for any part
Purchasing Management
- Purchase raw materials directly to the job
- Raise purchase orders for subcontract operations in a job
- Create manual purchase orders for miscellaneous items such as office supplies and services
- Add unplanned purchases directly to the job
- Track all outstanding orders, including backorders
- Measure and monitor delivery performance of suppliers
Shipping Management
- Ship goods to a customer from either a job or an order
- Ship goods directly from work in progress
- Print shipping and packing labels when you process a customer’s shipment
- Create shipments for miscellaneous items
- Add freight charges when you create a shipment
- Monitor your on-time delivery performance to your customers
- Report on all shipments due for delivery on a specified date
Labor Management
- Collect and control employees’ labor hours
- Define shifts with start and end times, grace periods, and payroll information
- Record critical information relating to each employee
- Track employees to see who has clocked in
- View the jobs currently in operation on the shop floor without physically visiting the factory
- Integrates with M1’s payroll module for a complete payroll function
- Verifies accuracy of timecards prior to payroll processing
Scheduling
- Control the shop floor with backwards and forwards scheduling of individual or multiple jobs
- View available capacity to overload situations for each work center or department
- Reschedule multiple jobs with a single screen
- Define a work center by its crew size, number of machines, etc.
- Provide a detailed Planned Material Requirements report
- Automatically schedule all assemblies within a job to come together for final assembly
Quality/Warranty Management
- Enter non-conformances to manage, control and analyze rework and scrap
- Manage the inspection process
- Quarantine parts under inspection
- Ensure recovery of costs on non-conforming material
- Process return authorizations and claims from customers
- Create, track, follow-up, verify and sign off on corrective and preventative actions
- Determine whether a claim is covered under warranty
System Security
- Control user access to company information
- View a complete audit trail of changes
- View the change type, date, user and view details of what changed
- Specify the report and component security